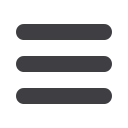
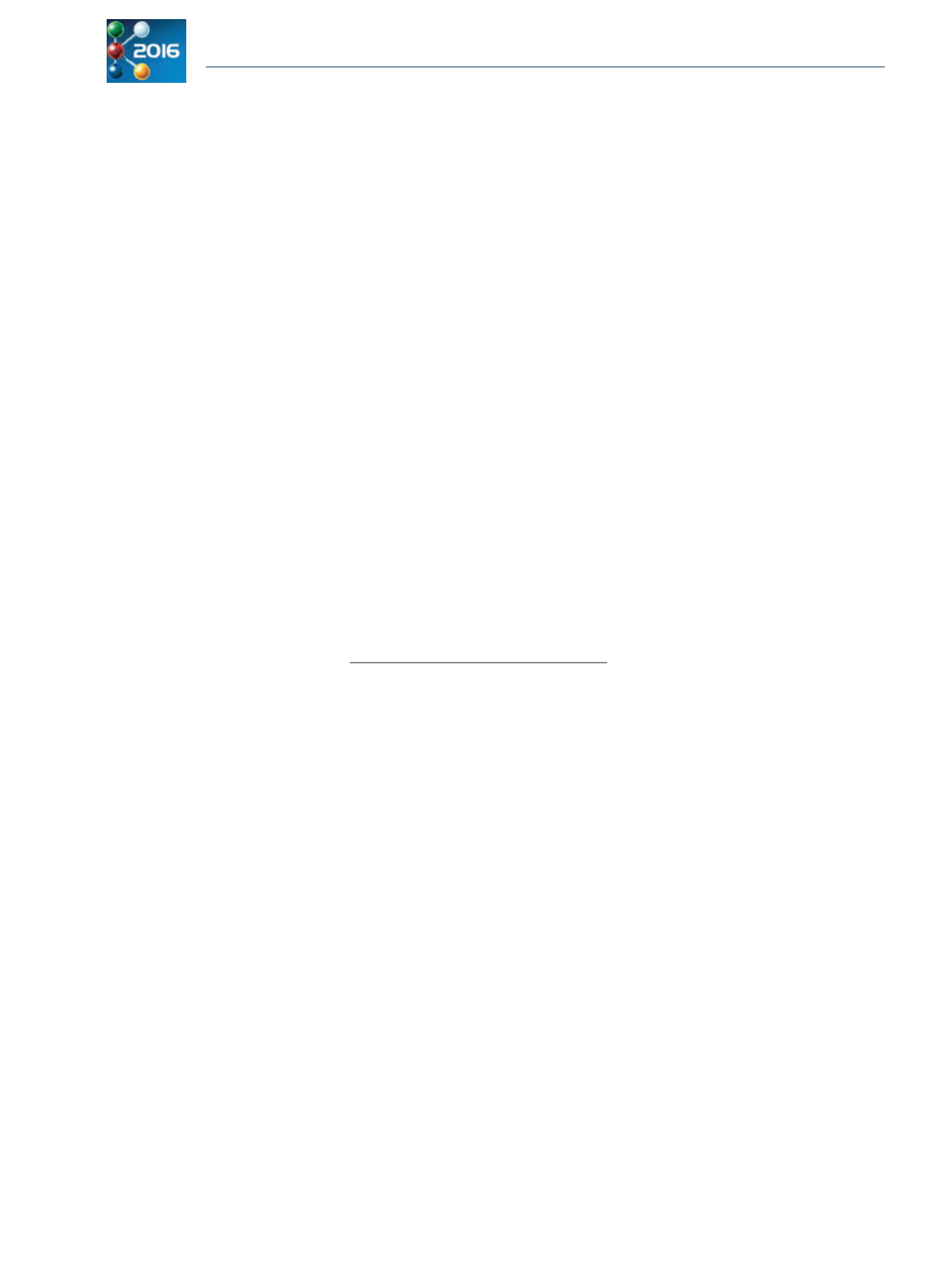
tendency of the film – may occur after ex-trusion. Extremely
uniform and controlled application of a minimal amount of
moisture compensates the tension and results in considerable
quality en-hancement.
Primer – the young and the wild
The application of primers for extrusion coating represents the
latest applica-tion area. For example, a bonding agent is re-
quired when a PE coat is co-extruded as sealing coat onto PET
film. With the WEKO application system this primer can be ap-
plied exactly and uniformly onto the carrier film, even at va-
riable speeds. Application of the primer takes place without
contact and is merely pulled into a uniform film through a
smoothing roller. Compared to the conventional method,
using anilox rolls and chamber doctor blade systems, minimal
and constant liquid application can be produced with the non-
contact WEKO process. Thanks to the minimal application, the
cost for the primer and also for the operation of the dryer can
be significantly reduced. Lower invest-ment costs and reduc-
tion of the process costs make the system particularly attrac-
tive for new facilities.
Rotor application systems – maximum precision
WEKO has specialized in applying finest surface films on ma-
terial webs. Rotors arranged in a row within a rotor carrier and
rotating at high speed ensure a non-contact application of li-
quids. The rotary movements of the rotors and the result-ing
centrifugal forces produce a uniform flow of finest micro-dro-
plets. This special technology allows the application of even
the smallest amounts of fluid precisely, reproducible and ad-
apted to the speed. In addition to its wide dynamic range,
these systems excel through outstanding service-friendliness.
WEKO application systems represent both highest industrial
requirements and also cost and ecolo-gy-minded production.
WEKO - Weitmann & Konrad GmbH & Co. KG
The WEKO experts offer support worldwide with the choice
and integration of WEKO non-contact minimal application sy-
stems in the production process. They help customers achieve
clear benefits and cost advantages with the ma-terials to be
processed and/or in the process itself. Comprehensive services,
such as test series at the WEKO technical centre and high
WEKO service standards, complete the WEKO offering.
In addition to the main office near Stuttgart WEKO maintains
two production locations in Germany and Brazil, own sales
and service subsidiaries in Italy, the United Kingdom, the U.S.,
and Brazil. Furthermore, WEKO collaborates worldwide with
agencies marketing the products and offering the proven WE-
KO service standard in addition.
Hall 4, Booth E25
➠ www.weko.netT
he specialist for optical measurement systems for geome-
try and surfaces on extruded profiles located in Mecken-
beuren, Germany comes up with a bundle of new products.
ASCONA has established itself as the world market leader in
geometry measurements for extruded profiles and is able to
provide optical measurement systems which can be used in
the laboratory as well as in the production environment.
The new starter models called PROMEX BASIC/ADVANCED
FAST work with a camera and an objective and therefore gua-
rantee measuring results within 2 to 5 s – irrespective of the
complexity of the profile.
The PROMEX EXPERT measurement instruments of ASCONA
are high-end solutions for geometrical measurements. The
PROMEX EXPERT back-light systems relevant for plastic and
rubber profiles meet highest requirements of measuring ac-
curacy in a minimum of measuring time. Thus fast corrective
actions to avoid scrap can be carried out. Generally, PROMEX
EXPERT systems are ideal for the use at the extrusion line be-
cause they are not sensitive to vibrations, temperature fluc-
tuations and dust.
ASCONA:
sets new standards
Recently ASCONA has also successfully launched a surface
measurement system for plastic profiles. The PROMEX CSI sy-
stem is interesting especially for manufacturers of visible pro-
files such as window profiles since it reliably detects grooves,
scratches, dents, inclusions, specks, marks or color pigment
faults. Directly integrated into the extrusion line PROMEX CSI
Inline records faults right where they occur. Thus a complete
sorting of defective sections of profiles is already guaranteed
in the production process.
The product range of surface examination is rounded off with
the PROMEX OBJECTIVE measurement system for web collap-
sing of extruded plastic profiles. From a certain dimension on-
wards, evenly shaped visible surfaces of plastic profiles need to
be supported by webs. However, webs may collapse during
the production process. Normally, these web collapses become
obvious only when linear contours appear on the surface. Ho-
wever, that is often too late for sorting out unusable profiles.
This is exactly where you can rely on PROMEX OBJECTIVE for
ensuring safety in your quality control process.
On the occasion of the K 2016 the latest products of ASCONA
Extrusion International 5/2016
72