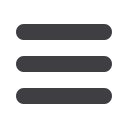
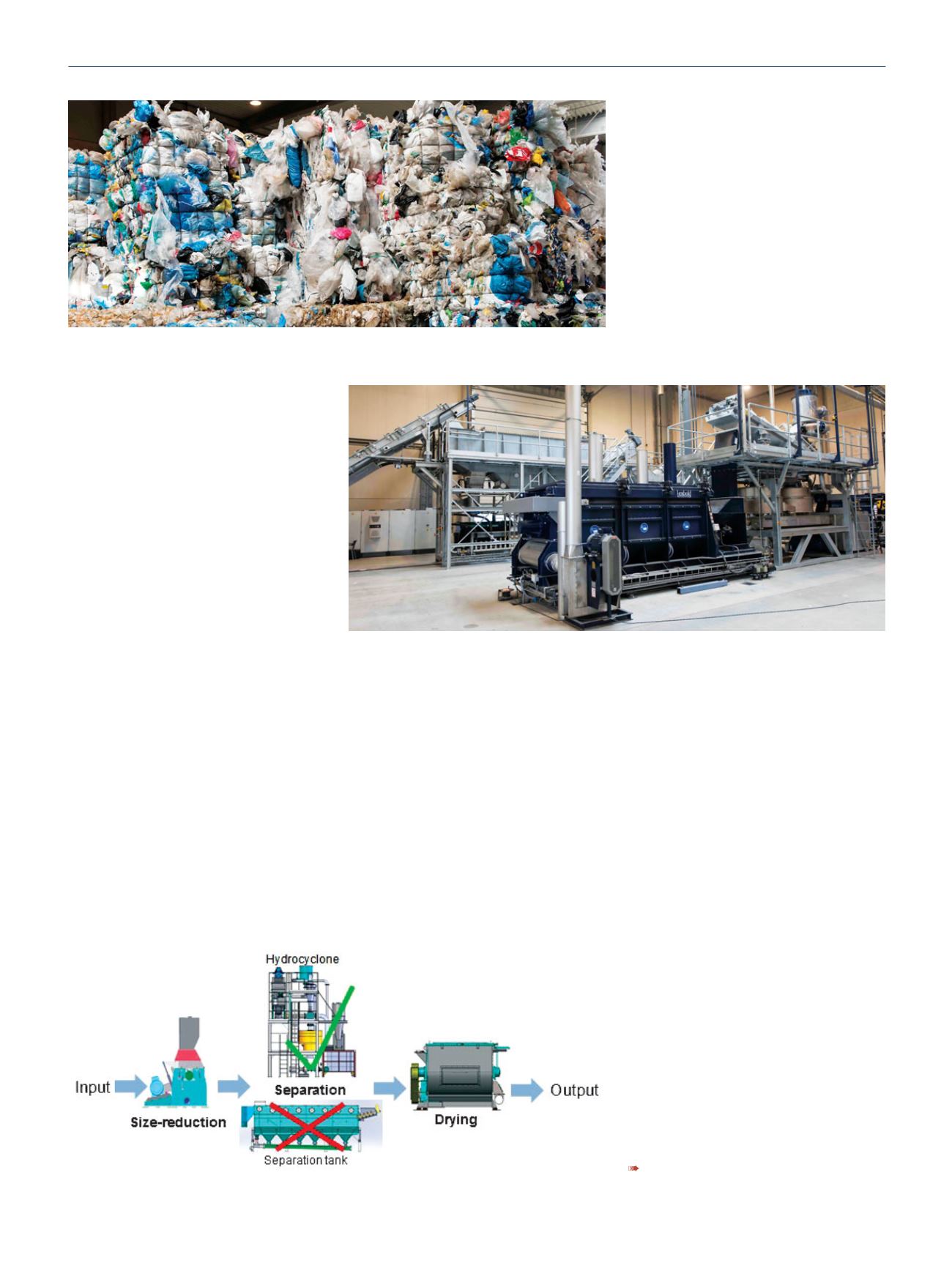
37
Extrusion International 4/2016
Approximately 25 years ago, Herbold
made the wet granulation technique
marketable and with it set standards
in the industry. The advantages of
wet granulation are obvious; less
wear and tear, no plastification due
to the optimum cooling during the
size reduction process, and a very ef-
fective separation from the first pro-
cessing step.
The Herbold Wet Shredder (fig. 1),
inside equipped with exchangeable
wear plates, shreds the infeed mate-
rial by the simultaneous addition of
wash water. The coarsest impurities
are already washed off during the
first process step.
Above all, this technique is well suit-
ed for highly contaminated mate-
rial such as agricultural film. It is also
suitable for post-consumer film from
households (fig. 2) and wet granula-
tion has significantly increased the
life between knife changes enabling
a more economic operation. Even
problematic material such as wood
and paper fractions inside the in-
put material can be handled better
through the wet shredding as water
allows for liberation from the mate-
rial early on in the process.
Further developments such as pre-
washing units, granulators with
forced feeding, hot wash steps with
ultrafiltration and hydro cyclone sep-
aration steps reduce energy costs,
process but also for the following
process steps in a washing line. The
washing line itself is no longer con-
taminated by extreme impurities,
hence the components have a longer
operating time and the final product
quality improves.
Retrofitting and upgrading of ex-
isting plants is an important topic –
HERBOLD MECKESHEIM assists with
expert technicians in order to incorpo-
rate the experiences of more than 300
installed wash and separation plants.
In the new technical center inMeckes-
heim near Heidelberg where current-
ly extensive enhancements are carried
out HERBOLDMECKESHEIMdevelops
solutions in collaboration with the
customer. A first trial with the cus-
tomer’s original material is free of
charge; the tests are processed with
machines in industrial scales.
Engineering, Manufacture, Delivery:
Pic. 2: Post-consumer film
Pic. 3: Hydro cyclone and Dryer, in the background Pre-washing unit
Pic. 4: Flowsheet Herbold Meckesheim
www.herbold.comfresh water and energy consumption
and increase at the same time the
quality of the final product.
The Herbold Pre-washing unit VWE
600/2 separates e. g. foreign bod-
ies such as stones, metals, glass and
sand using three different integrated
process steps. The feeding material
undergoes an intensive washing step
and then, in a third step, makes fur-
ther foreign material sink.
Both process steps reduce the wear
and maintenance costs not only for
the first step in comparison to a dry