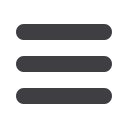
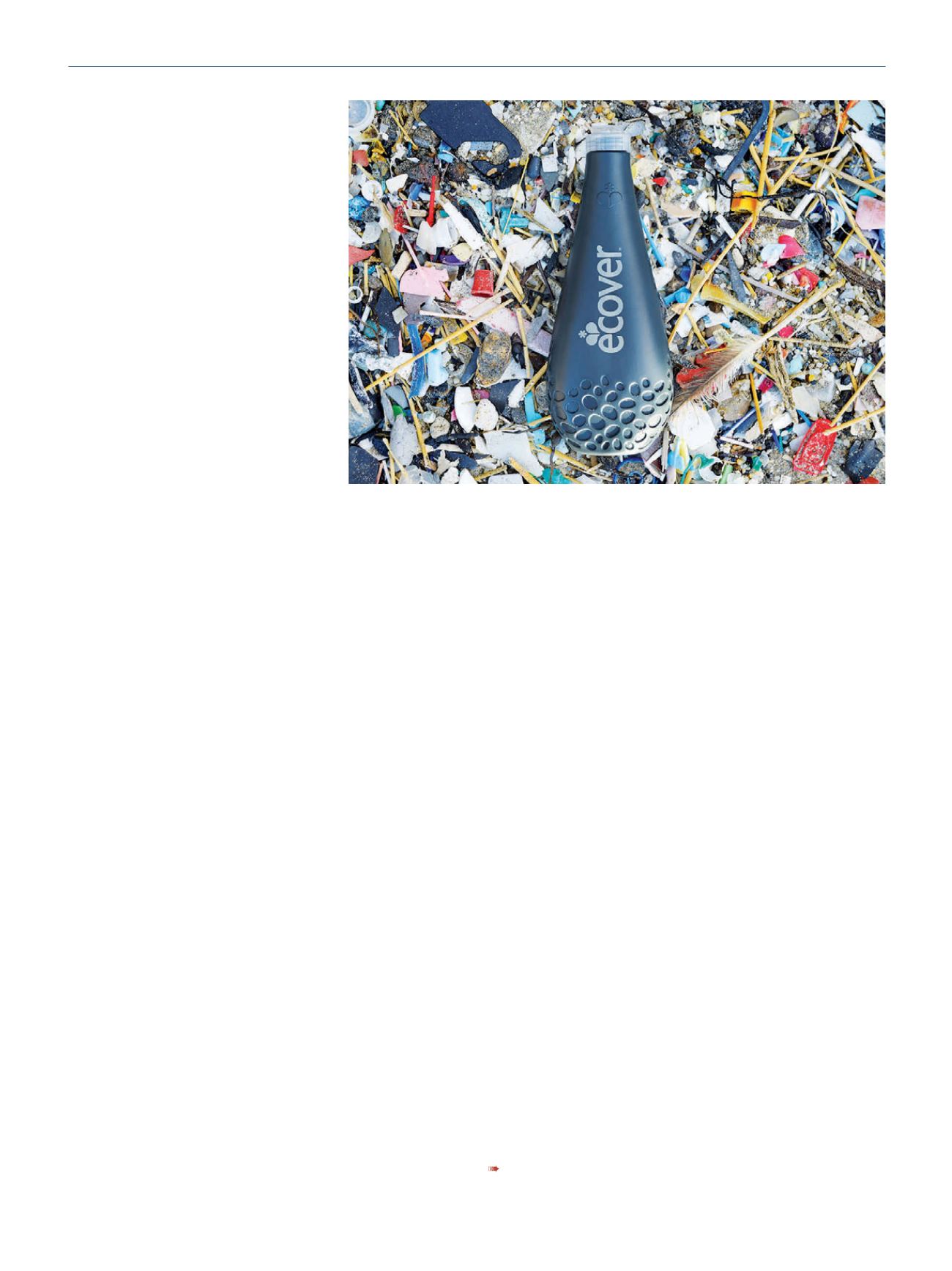
43
Extrusion International 4/2016
of post-consumer wastes. With the aid of the RecyClass
(www.recyclass.eu) programme, any manufacturer of
plastics packages can quickly and easily check whether his
package is recycling-friendly. Here it is particularly impor-
tant to dispense with fillers like chalk in PE and PP pack-
ages as far as possible, avoid plastics-paper composites,
use pigmentation in moderation and make sure that the
density of all products is well clear of 1 g/cm³ so that sepa-
ration on the basis of density is possible.
At the same time, efforts are being made in the indus-
try to develop reutilisation strategies for mixed wastes.
Trenntechnik Ulm GmbH is pursuing a very exciting ap-
proach here in developing a chemical separation process
for PE/PA composite films and building a unique produc-
tion plant with a capacity of 10 tonnes per day. The end
products of the separation process are a polyamide com-
parable with virgin material and a polyethylene that is
pigmented directly with soot, i.e. a carbon black master
batch in a particularly pure form. As stressed by Manag-
ing Director Wolfgang Zacherle, there is a suitable sol-
vent and separation agent for every plastics composite,
so there are no obstacles to an extension of this process
to other composite products.
Summary
Although recycling is a much-discussed topic today and is
also very much alive in many projects in the plastics indus-
try, experts are repeatedly confirming that, by compari-
son with other sectors, too little waste material is used
instead of virgin material. Across Europe, 50 per cent of
metal scrap is returned to the steelmaking process, and
the same applies to the paper industry, where 50 per cent
of old paper and board is used in the production of new
paper and board. For glass, at 33 per cent, the figure is a
little lower, but still very high compared to the quantities
that are recycled in the plastics sector. For in the plastics
sector, only about 4 per cent of reprocessed waste plastics
are used instead of virgin material in the fabrication of
plastics products. The plastics sector is of course a young
industry overall. Plastics only became widespread in the
1950s, and reutilisation strategies for waste plastics were
only introduced in 1990s, yet both the collection systems
and technical feasibility have developed enormously in
the intervening period. Anyone wishing to find out about
these new technical solutions can do so at K 2016, the
world’s No. 1 trade fair for the plastics and rubber indus-
try, from 19 to 26 October in Düsseldorf. Numerous ex-
hibitors are presenting machines and plant for processing
and recycling, for pure-grade wastes as well as for mixed
wastes and wastes of rubber.
It can therefore be assumed that recycling rates will contin-
ue to rise in the years to come, as there is strongdemand for
recyclate for both environmental and economic reasons.
Marine litter, i.e. the pollution of the seas with wastes, has
internationally highlighted the irresponsible treatment of
wastes particularly in newly industrialised countries and
lent added strength to the demands of other consumers
for the sustainable treatment of resources. Model projects
like the Ocean Bottle are not only very interesting exam-
ples, but also help to raise awareness of the subject among
the general public and, above all, consumers. For the pro-
duction of this Ocean Bottle, Ecover Belgium N.V. enlisted
the services of fishermen in Britain, France and Belgium to
collect bottles from the sea. 10 tonnes of waste was accu-
mulated within a year, and the PE fraction from this was
recycled into new PE dishwashing detergent bottles.
www.k-online.comFor the extrusion blow-moulded
dishwashing detergent bottle made
of polyethylene, Ecover Belgium N.V.,
manufacturer of ecological cleaning
agents, uses plastic wastes gathered by
fisherman from the sea. Image: Ecover