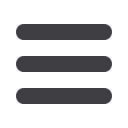
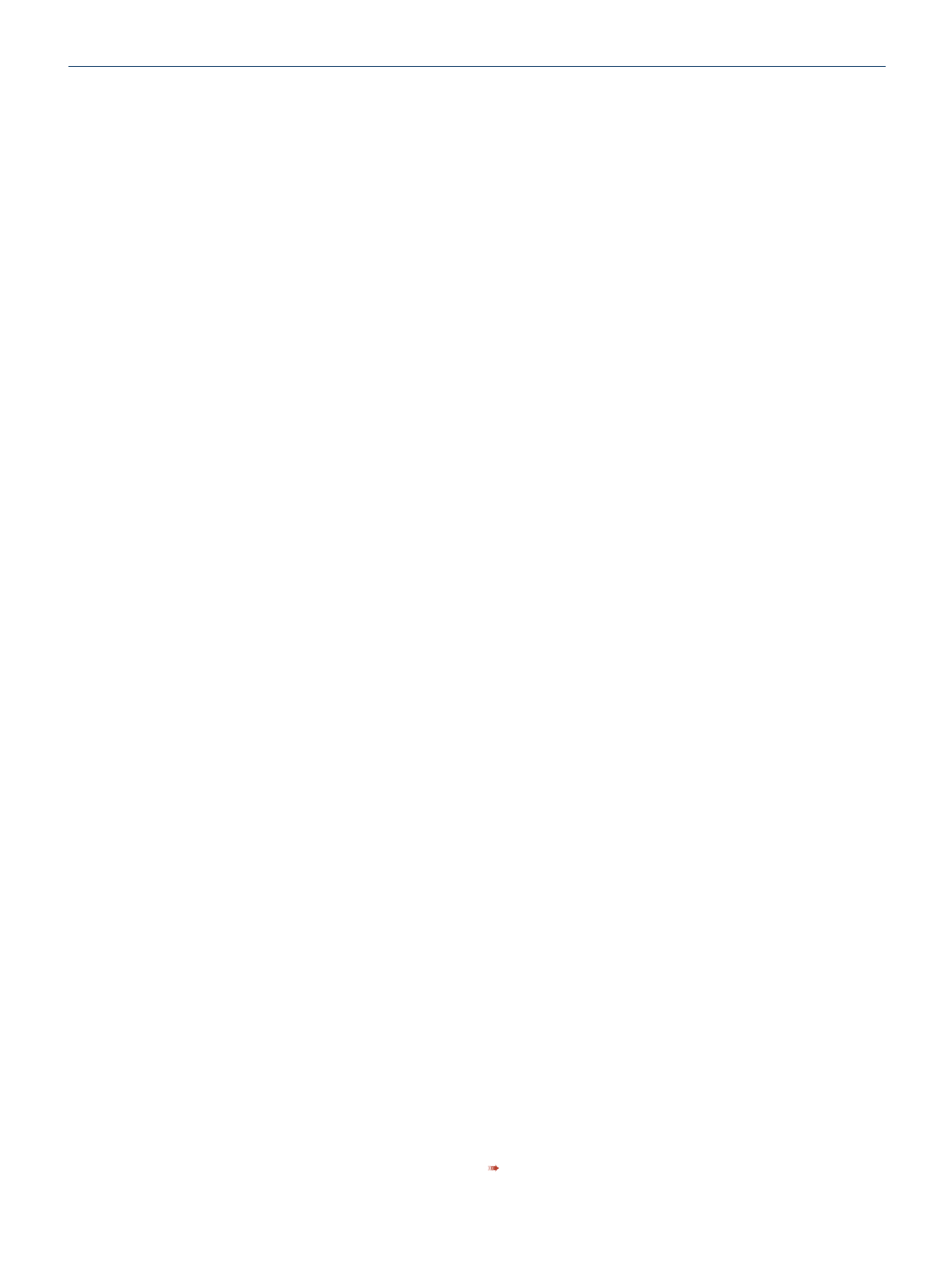
29
Extrusion International 1/2017
materials and no coupling medium is needed. The tech-
nology is independent of the temperature of the mate-
rial, what makes it possible to integrate an X-ray mea-
suring device directly into an extrusion line without any
additional efforts. A calibration is not necessary. The
system is either installed directly after the extruder (hot
measurement) or at the end of the line (final quality con-
trol). With a 4-point online measurement, the measuring
values for the wall thickness, the eccentricity, the inner
and outer diameter and the ovality are determined by
one device. The system measures up to three different
material layers. These measuring values are visualized
numerically and graphically in the form of the tube/pipe
cross section in real-time and enable the user to perfectly
center the extrusion tool. Important for highest efficiency
is the automatic control of the line speed or extruder rpm
while considering the minimal values. Thus, the quality
of the hose is ensured. On the other hand, the control to
the minimal values ensures that only the needed material
is used. X-ray technology is available for products with a
diameter from 0.65 to 270 mm. Concerns on the safety
of X-ray devices are arbitrary, as the radiation is because
of the low energy of no relevance. Practically, a human is
exposed to a much higher radiation on a flight from New
York to Frankfurt.
Technologies for the measurement of large plastic pipes
For the dimension measurement of large plastic pipes
starting at a diameter from 110 mm, as they are found in
the building and service area, the above-described tech-
nologies can be used. Nevertheless, these technologies
reach their limits either functionally (ultrasound) as well
as regarding the costs, the limited measuring range and
number of measuring points on the circumference (X-ray)
or the limitation in the measurement of the diameter only
(laser). A further technology for the quality control is cur-
rently tested. It uses terahertz pulses, which activate a
powerful fiber laser that is aimed at the material. The wall
thickness is determined by means of the reflected echoes
from the inner and outer boundary layers. The usage of
this technology for the measurement of larger wall thick-
nesses and materials with a high damping, as for example
PVC, are however limited. Furthermore, the durability of
the laser is limited and the costs are very high.
Millimeter waves technology
An innovative, significantly less expensive technology for
the dimension measurement and recording of the sag-
ging is the radar technology FMCW (Frequency Modu-
lated Continuous Waves). These systems work within
the sub-terahertz range and are already used for some
time in the automotive technology for distance measure-
ment. They are based on semiconductor technology, are
inexpensive and practically not limited regarding their
lifespan. Within the chosen area from 80 to 300 GHz all
plastic materials are penetrated with low absorption and
thus, the wall thickness is measured. One or two continu-
ously rotating transceiver continuously send and receive
frequency modulated millimeter waves while moving
around the tube. As an alternative, a static system mea-
sures selectively the wall thickness and outer and inner di-
ameter of a tube with two transceiver at 4 points. A rotat-
ing gauge head is used when the complete measurement
of the wall thickness around the whole circumference of
the tube is required. In this version, also the sagging is
measured and displayed precisely. The measurement uses
the time difference of the signals that are reflected by the
boundary layers of the front and back site of the plastic
material. The measurement is realized with an accuracy
of few micrometers and a measuring rate of 500 single
measurements per second. The millimeter waves tech-
nology measures products with a diameter from 110 to
3,000 mm precisely, around the complete circumference,
with no need for coupling medium and is not influenced
by the temperature or plastic material. Furthermore, the
measuring system adapts the properties of the extruded
plastics by itself – a calibration by the user is redundant.
Furthermore, the technology provides information for
centering the extrusion tool and thermal control of the
line. Thereby, the measuring values are used to ensure an
optimal concentricity and minimal wall thickness.
Summary
With the increasing quality requirements at the produc-
tion of hoses and tubes, the precise and reliable quality
control for plastic pipes at the extrusion by a Non-De-
structive Testing (NDT) becomes significantly important.
Furthermore, an efficient usage of materials for costs sav-
ings is in focus of the plant management. Measuring and
control systems monitor and control important product
parameters continuously. Thereby, hose and tube manu-
facturers may choose from various technologies with dif-
ferent functions and diverse applications.
The laser technology offers a reliable online measure-
ment of the diameter from 0.05 to 500 mm. Additionally,
X-ray measuring systems measure the wall thickness and
eccentricity of products with a diameter up to 270 mm.
A further innovative technology, based on millimeter
waves, is used for extrusion lines where large plastic pipes
up to 3,000 mm are produced. The technology is appli-
cable for different material types and measures common
tube dimensions as well as the sagging precisely. Which
measuring technology should be used in an extrusion line
depends, therefore, on the application area and the re-
quirements of the user regarding measuring and control
technology for quality assurance, process optimization
and cost savings.
www.sikora.net