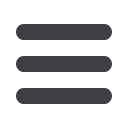
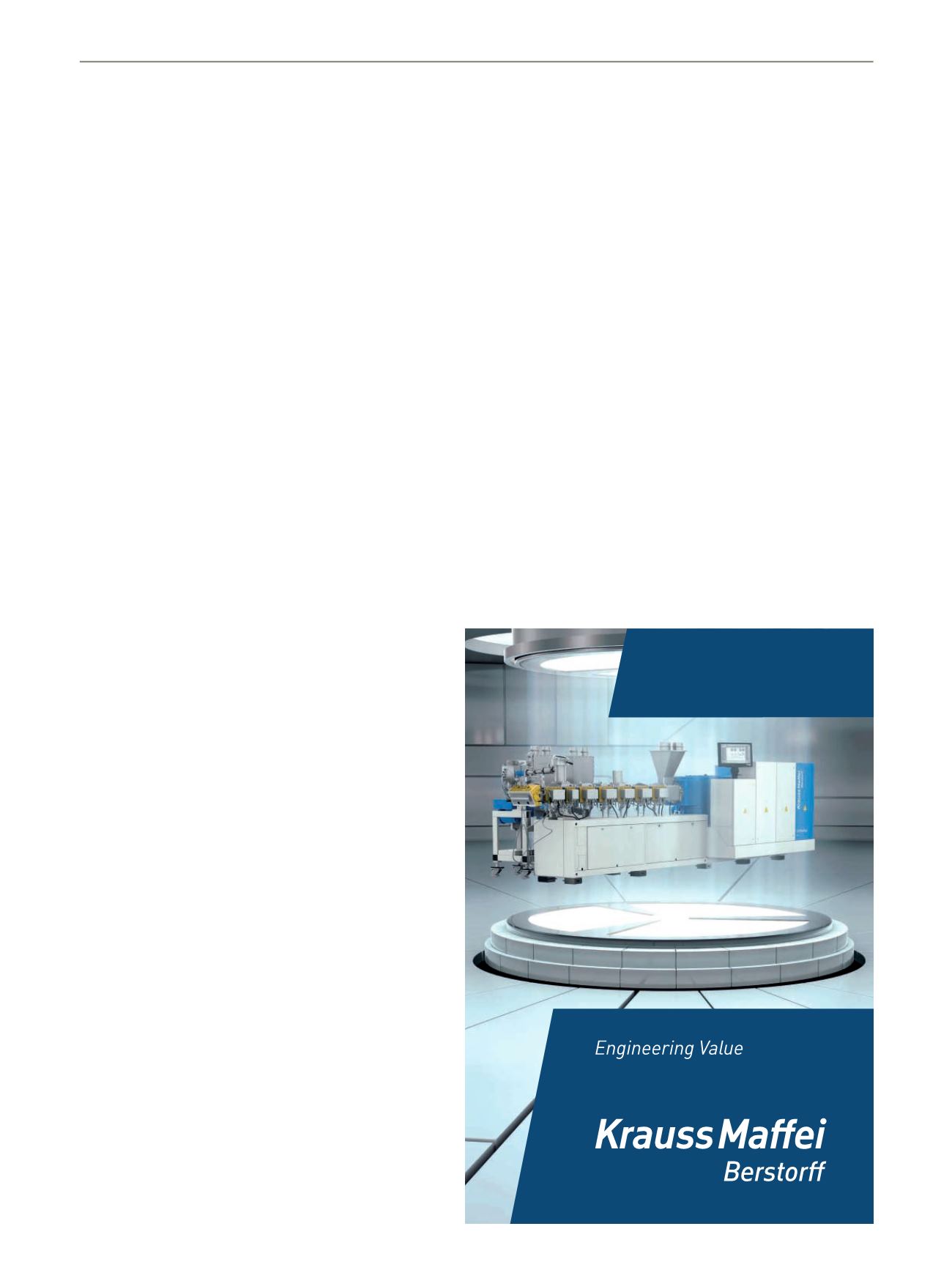
damage without limiting throughput. It is cost-competi-
tive and can even be retrofit to existing systems.
The new FLX-128 Plus system, which will be set up to
control the R-PRO demonstration, is scalable and has all
the same features that made the previous web-enabled
FLX-128 Conair’s most popular conveying system control,
but now is smarter, faster, and more powerful. It not only
can control R-PRO systems, but also integrates Conair’s
newest line-proofing systems including the Invisible Line
Proofing (ILP) system mentioned below. The FLX-128 Plus
flexible control system utilizes a combination of centra-
lized I/O and expansion modules, interconnected via in-
dustrial Ethernet to provide control of up to 128 recei-
vers, 40 pumps (plus 2 back-up pumps) and 256 source
valves. A full color touch screen with descriptive icons en-
sures that even with little or no training, any user will be
comfortable monitoring or making changes on up to 40
independently operating vacuum systems.
For the first time anywhere, a mobile drying/conveying
system (MDCW) will be shown with Conair’s newest DC-
A touchscreen control interface. The MDCW combines
an efficient Carousel
®
Plus Dryer with a conveying
blower, dust collector and direct-feed vacuum receiver to
convey dried material to the throat of a processing ma-
chine – all assembled on a safe, convenient wheeled cart.
Featuring intuitive graphical design, with minimal text
and no function codes to decipher, the DC A touchscreen
control has descriptive help screens for operators and
features auto-start capabilities, password protection and
has Conair’s Drying Monitor capabilities built in. Trending
capabilities simplify maintenance and troubleshooting,
while providing users with information they can use to
optimize drying parameters and save energy. The new
DC-A control will also be offered on smaller Conair desic-
cant-wheel dryers.
The new MedLine
®
family of clean-room-ready products
was developed to help medical plastics processors select,
install, commission and start up white rooms and clean-
rooms faster and with less paperwork. It includes a com-
plete range of auxiliaries – 40 different models and 170
different configurations in all – for molding and extrusion
of medical products. The design of MedLine conveying,
storage, drying, blending, heat-transfer and downstream
extrusion products are all based on proven Conair de-
signs, but they have been specially sized, configured, do-
cumented and supported for use in cleanrooms and
other controlled environments.
Conair MedLine products at K 2016 will include a MedLine
MicroWheel dryer. Thought to be the smallest desiccant
wheel dryers available, they offer an alternative to com-
pressed-air dryers and small twin-tower units, making
them ideal choice for medical processors and others run-
ning small quantities of expensive engineering resins. The
mini dryer will be fitted with a MedLine TubeLoader, a
compact, self-contained loader with built-in vacuum mo-
tor that can convey 150 lbs/hr (68 kg/hr) nearly 20 ft (6 m).
Also shown in the MedLine configuration will be a TB-45
TrueBlend™ gravimetric blender mounted on a floor
83
Extrusion 6/2016
www.kraussmaffeiberstorff.comDie Baureihe ZE BluePower bietet Ihnen inno-
vativste Lösungen, speziell und flexibel auf Ihre
Compoundieraufgaben zugeschnitten.
30 % mehr Drehmomentdichte bei über 23 % mehr
Volumen* beamen die ZE BluePower in eine neue
Effizienzklasse durch 30 % mehr Durchsatz* bei
geringstem Energieeinsatz.
*Im Vergleich zur Vorgängergeneration gleicher Baugröße
Compoundieren
der Zukunft:
Der neue
Zweischneckenextruder
ZE BluePower mit
maximaler Leistung und
vergrößertem Volumen
Besuchen Sie uns auf der K 2016:
Halle 15, Stand B27 / C24 / C27 / D24
19. – 26. Oktober 2016
Düsseldorf