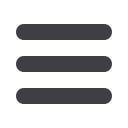
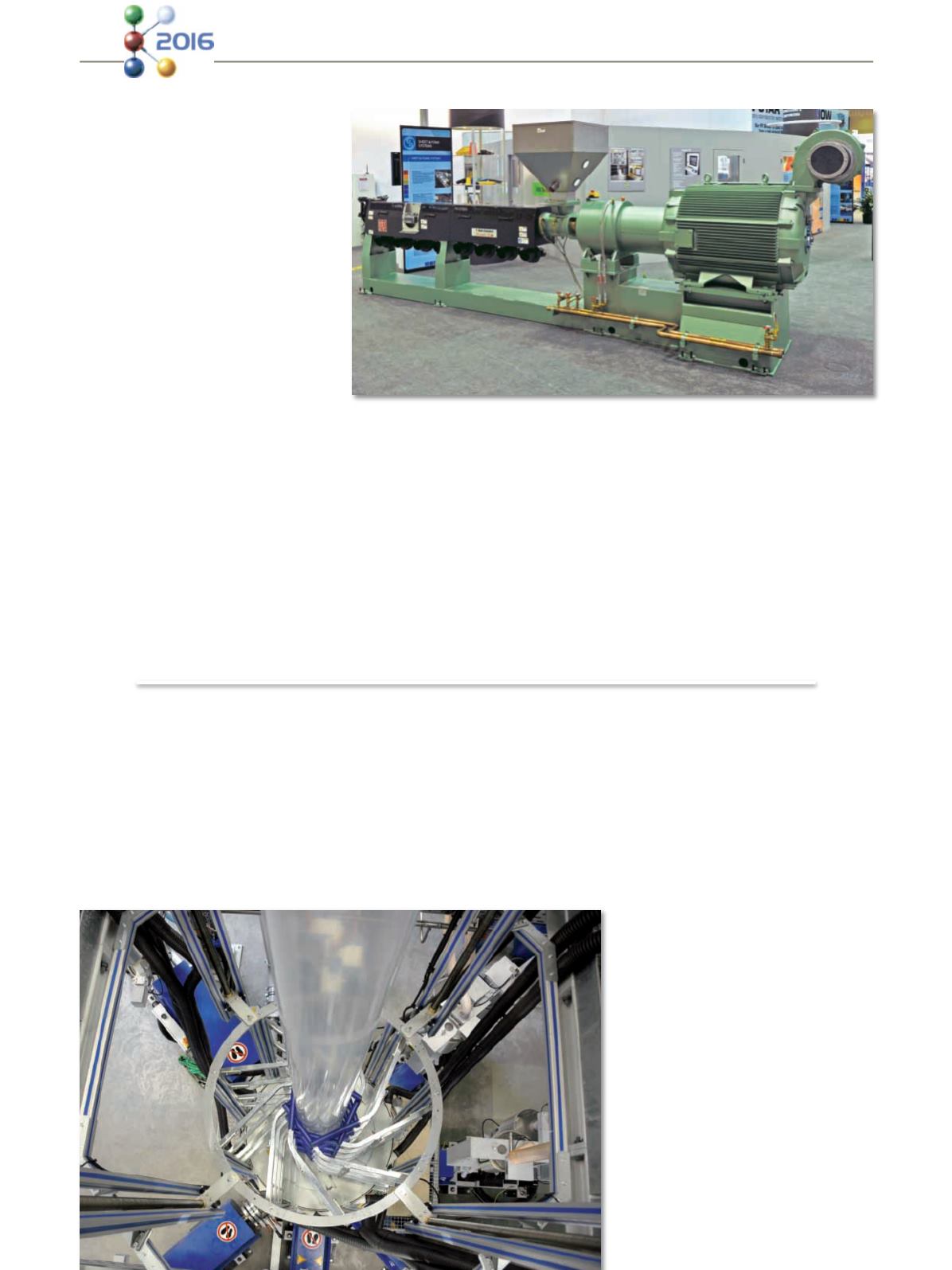
90
Preview
Extrusion 7/2016
➠
Davis-Standard, LLC
www.davis-standard.comK 2016: Halle 16, Stand A43
throughput rates up to 1,500 kilograms
per hour (3,300 pounds per hour). It has
also shown increased performance den-
sity for PP and PS extrusion. We look for-
ward to discussing these benefits with
customers during the show.”
Davis-Standard’s 75mm, 40:1 extruder
offers processing versatility due to a fa-
vorable surface to volume ratio when
compared to conventional extruders. The
extruder can be supplied with a direct
drive AC motor or permanent magnet
n
The efficiency and throughput capabi-
lities of Davis-Standard’s high-speed ex-
trusion technology will be promoted dur-
ing K 2016. Davis-Standard is one of on-
ly a few manufacturers worldwide to of-
fer a high-speed extruder for demanding
processes where rates and energy sav-
ings significantly impact profitability. Ad-
vantages such as better product quality,
less machine volume for reduced
changeover time, and a wider processing
window are just a few reasons high-
speed extrusion is a cost-effective op-
tion.
“We’ve supplied high-speed technology
for awhile, but there is still a lot of op-
portunity for those who seek new ways
to boost throughput and performance,”
said Steve DeAngelis, Davis-Standard
Vice-President of Sheet and Foam. “The
potential for improved processing is
especially evident for high-speed sheet,
fiber and extrusion coating processes.
Our design has demonstrated excellent
thermal stability and melt quality at
High-Speed Extrusion
synchronous motor configuration. Davis-
Standard’s high-speed model offers
energy savings of 10 to 15 percent when
compared to traditional systems. Addi-
tionally, the screw speed and drive unit
can be adjusted to accommodate diffe-
rent processing conditions. Davis-Stan-
dard has done extensive work on screw
designs to further support performance.
logisch abbaubaren Folie von BASF sowie
einer Mailingfolie in Zusammenarbeit mit
Total.
Dass die allseits verwendeten HDPE-Fo-
lien in Form der hauchdünnen Hemd-
chen-Tragetaschen für Frischprodukte in
der Kritik stehen, ist einer der Gründe für
die neuen ökologisch orientierten Folien,
wie sie derzeit vor allem in Europa gefor-
n
Auf der POLYREMA-Hausmesse zur
K 2016 werden auf einer Anlage Ein-
schicht-Blasfolien ("Mono") unter Pro-
duktionsbedingungen getestet: Am ers-
ten Tag mit der Produktion einer Folie
aus HDPE, am zweiten Tag mit einer bio-
Ultraleichte Tütenfolie
dert werden. Dazu Manfred Kurscheid,
Geschäftsführer POLYREMA: „Tüten aus
dieser Folie können nach dem Einkauf als
Biomülltüte weiterverwendet oder kom-
postiert werden. Mit dieser neuen Anla-
ge können also beide Folienarten herge-
stellt werden: die klassische ebenso wie
die biologisch abbaubare!“
Die ultraleichte Tütenfolie steht indes
nicht allein im Mittelpunkt der Hausmes-
se. POLYREMA demonstriert, dass Ein-
schicht-Anlagen noch deutlich mehr
leisten können: Durch eine zusätzliche
Ultra-Flat-Plus-Einheit entsteht eine
hochqualitative und deutlich festere und
in der Planlage verbesserte Folie, die la-
miniert und kaschiert werden kann. Da-
zu Marcel Perrevort, Vertriebsleiter der
POLYREMA: „Diese Folie lässt sich auch
mit Papier laminieren, so dass zum Bei-
spiel die typische Wickelfolie für Butter-
verpackungen oder Metzgereibedarf
entsteht“.
7 Schicht Micro Anlage in Produktion