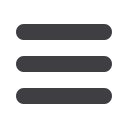
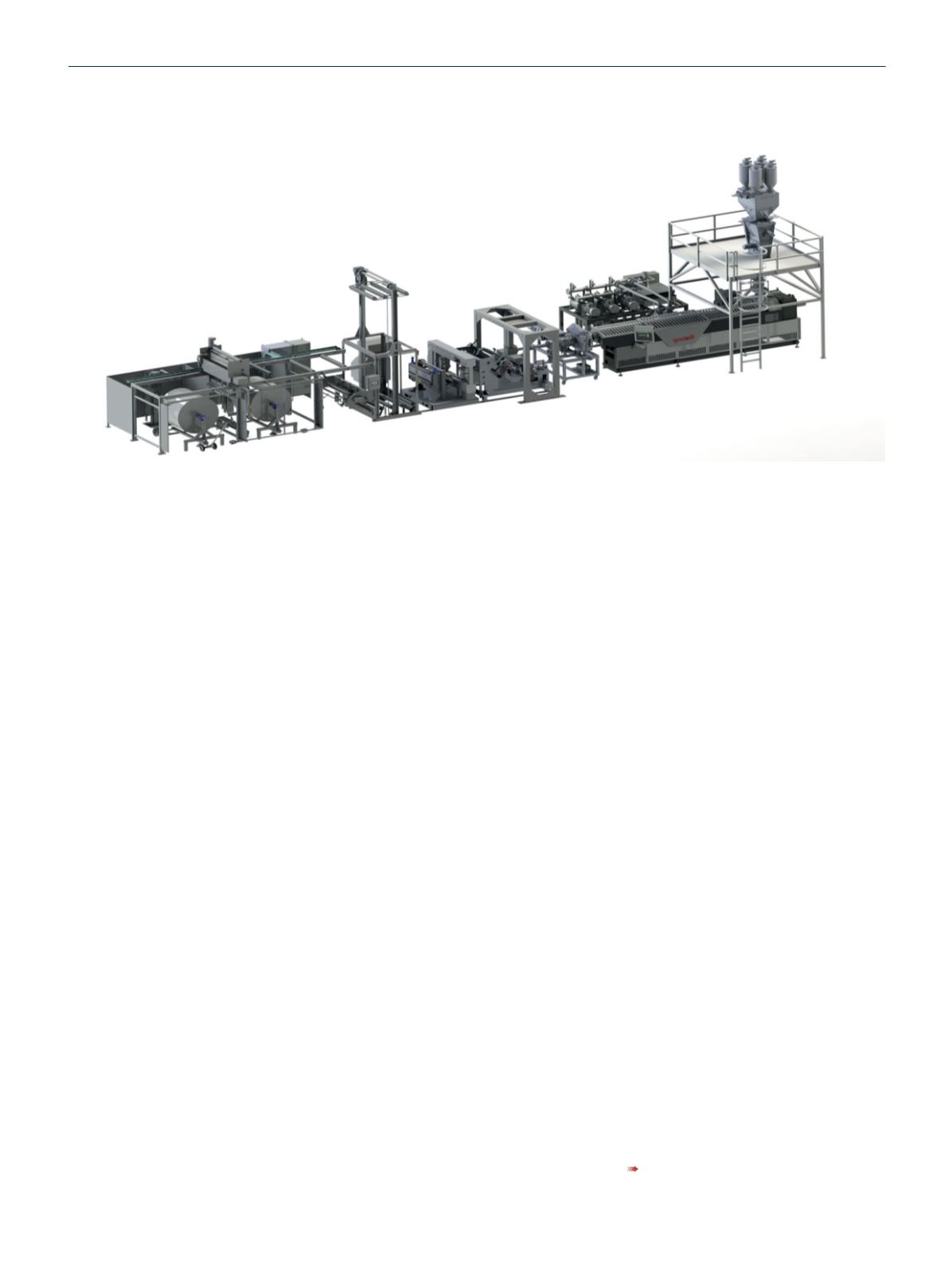
27
Extrusion International 4/2016
PET SHEET EXTRUSION
high polymer surface exchange rate under
vacuum in the MRS section, a vacuum level
of only 25 bar is required in order to achieve
100 % moisture extraction. Another effect
of the extremely high polymer surface area
exchange rate under vacuum is the excellent
extraction of volatile contaminants. The sys-
tem achieves the requirements of both the
FDA and EFSA without restrictions PET sheet
made on the MRS extruder is therefore suit-
able for food contact applications whatever
input material is used and without any pre-
treatment of the input material.
The Gneuss Processing Unit includes also the
unique Gneuss Rotary Melt Filtration System
for the efficient removal of solid contami-
nants with fine filter elements even on post-
consumer bottle flake. The Gneuss Online
Viscometer ensures a consistent, defined IV
value of the polymer thanks to the intelli-
gent control system and is an extremely use-
ful tool for quality monitoring and control.
Gneuss offers complete lines including the up-
and downstreamcomponents fromthemate-
rial dosing system to the die, roller stack and
to the winder, which are all tailored to the ex-
act requirements of the individual customer.
As Dr. Carl-JürgenWefelmeier (Manager Busi-
ness Unit Film and Sheet) was pleased to in-
formus: “We are very proud that we can offer
turnkey PET sheet extrusion lines – from the
project engineering to After-Sales-Service”.
Gneuss can offer individual systems, whether
it be for the replacement of existing, conven-
tional extruders in existing lines with Gneuss
Processing Units or the design, supply and
commissioning of a complete new PET sheet
line. In each case, sheet with a high transpar-
ency and gloss, extremely low haze and low
yellowness with good thermoformability
can be made with great efficiency.
The complete sheet extrusion lines are highly
flexible with regard to the input material and
with regard to the sheet which can be made
on them, inlcuding even sheet for optical ap-
plications.
www.gneuss.comWithin the packaging industry, the use of
PET sheet is on the increase and the use of
recycled material is likewise on the increase.
Whether the PET sheet is used for transpar-
ent packaging for food (trays or tubs for
fruit, vegetables, meat, cookies etc.) or for
non-food (such as blister packaging) it is al-
ways important to take account of the par-
ticular properties of PET and it is exactly this
which Gneuss has done.
With the Multi Rotation System (MRS) Ex-
truder, Gneuss has developed the only ex-
truder specifically designed not only with
the material PET in mind, but with the repro-
cessing of PET. With the MRS extruder Gne-
uss offers a processing unit which enables
PET to be extruded cost effectively, without
any pre-drying or crystallisation. This applies
both to the processing of both virgin and
post- consumer bottle flake with a residual
moisture level of 1 % and in some cases
more. The extruder will also easily handle
PET / PE scrap (laminated sheet) andmixtures
of PET and PETG. Thanks to the extremely
Gneuss Thermoforming Sheet Line
Increased Flexibility and Food
Contact Certification
Machinery manufacturer from Bad Oeynhausen (Germany)
delivers complete, tailor-made PET Sheet Lines
In the worldwide growth industry of PET packaging sheet,
Gneuss has installed over 20 tailor-made sheet lines over the
last few years. Gneuss´ customers find the extreme flexibility of
the Gneuss Processing Unit (GPU), consisting of MRS extruder,
Rotary Filtration System, Online Viscometer and Control System
completely convincing when processing PET, whether virgin or
recycledmaterial andwithorwithout foodcontact requirements.