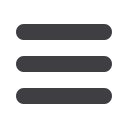
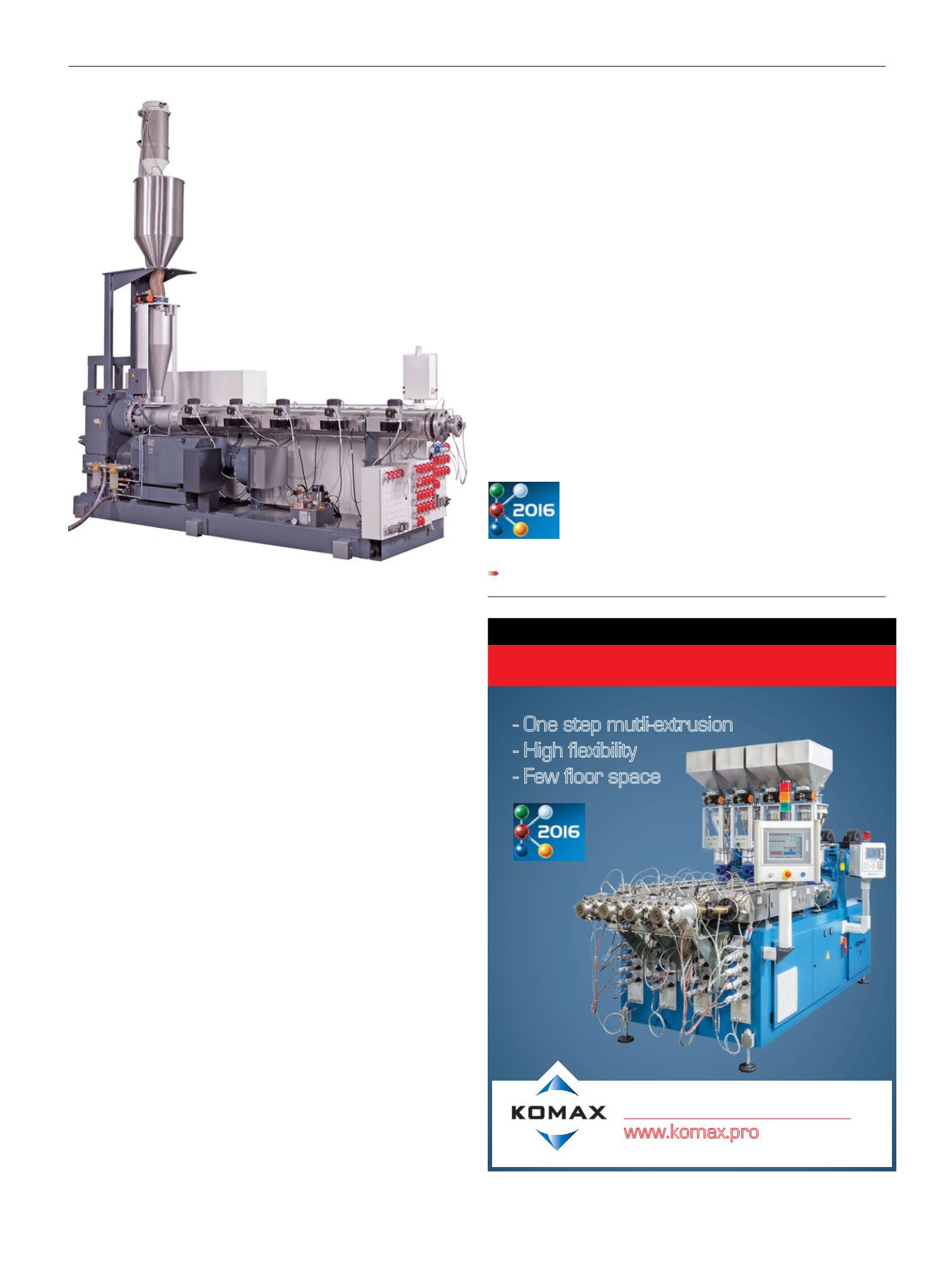
25
Extrusion International 4/2016
Based on the proven solEX 40 D extruder series, which
had alrea-dybeen designed for high-performance appli-
cations, the battenfeld-cincinnati engineers have now
successfully developed a new groundbreaking process-
ing unit. Barrels, screws, and grooved bush have all been
completely redesigned.
The major changes are an internally grooved barrel, a
screw con-cept that consistently applies the theory of dis-
persive melting, as well as a feed zone with a completely
revised geometry and fitted with spiral grooves. All three
components are ideally matched, thus enabling a further
improvement in the process attributes.
The solEX NG extruder series is available in four sizes (60,
75, 90 and 120 mm) and offers outputs ranging from
1,000 to 2,500 kg/h – an increase of up to 25% for each
machine size compared to the original solEX series.
One of the benefits offered by the innovative design
of the processing unit is an increase in melting capac-
ity, along with gentle and energy-efficient processing.
Thanks to this, the melt tem-perature in the extruder is
reduced by up to 10°C for comparable outputs, while the
melt homogeneity remains at a consistently high level.
The modification in the conveying mechanism leads to a
significant reduction of the axial pressure profile in the
feed zone and the barrel, thus reducing pressure across
the entire system and enabl-ing an increase in the specific
output level. In addition, the proces-sability of regrind is
improved, so that higher amounts of regrind can be pro-
cessed without impairing process behavior. Furthermore,
it is expected that wear behavior will also significantly im-
prove, which contributes to considerably higher process re-
liability when using critical materials. Less wear means low-
er maintenance costs and consequently higher efficiency.
In this context, the reduction of energy consumption
thanks to the new processing unit is another decisive fac-
tor. Energy cost savings of up to 15% are possible: Firstly,
less drive energy is required and, secondly, due to the
cooling of barrel and grooved bush sig-nificantly less heat
discharge is necessary. And the new processing unit of-
fers yet another advantage: As the basic structure of the
extruder was retained from the previous series, existing
solEX models can be retrofitted with the innovative NG
processing unit.
The solEX NG series not only complements the wide range
of bat-tenfeld-cincinnati single and twin screw extruders,
but also the portfolio of solutions for large-diameter pipe
extrusion, where bat-tenfeld-cincinnati is the technology
leader. The solEX NG extruders with their high outputs
and excellent melt processing capacities are ideally suited
for PO pipe lines with diameters of up to 2.6 m.
www.battenfeld-cincinnati.comThe design of the solEX NG extruder series
is nearly identical to the proven solEX
range. This makes it possible to retrofit
existing machines with the new process
technology (photo: battenfeld-cincinnati)
Hall 16, Stand B19
0 X O W L 6 W U D Q G ( [ W U X V L R Q / L Q H
+ ( / , % $ 5
7 ( & + 1 2 / 2 * , (
2QH VWHS PXWOL H[WUXVLRQ
+LJK IOH[LELOLW\
)HZ IORRU VSDFH
UXH GX 0DLQH
:,77(1+(,0
7pO
)D[
ZZZ NRPD[ SURLQIR#NRPD[ SUR
Hall 16,
Stand F29