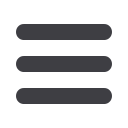
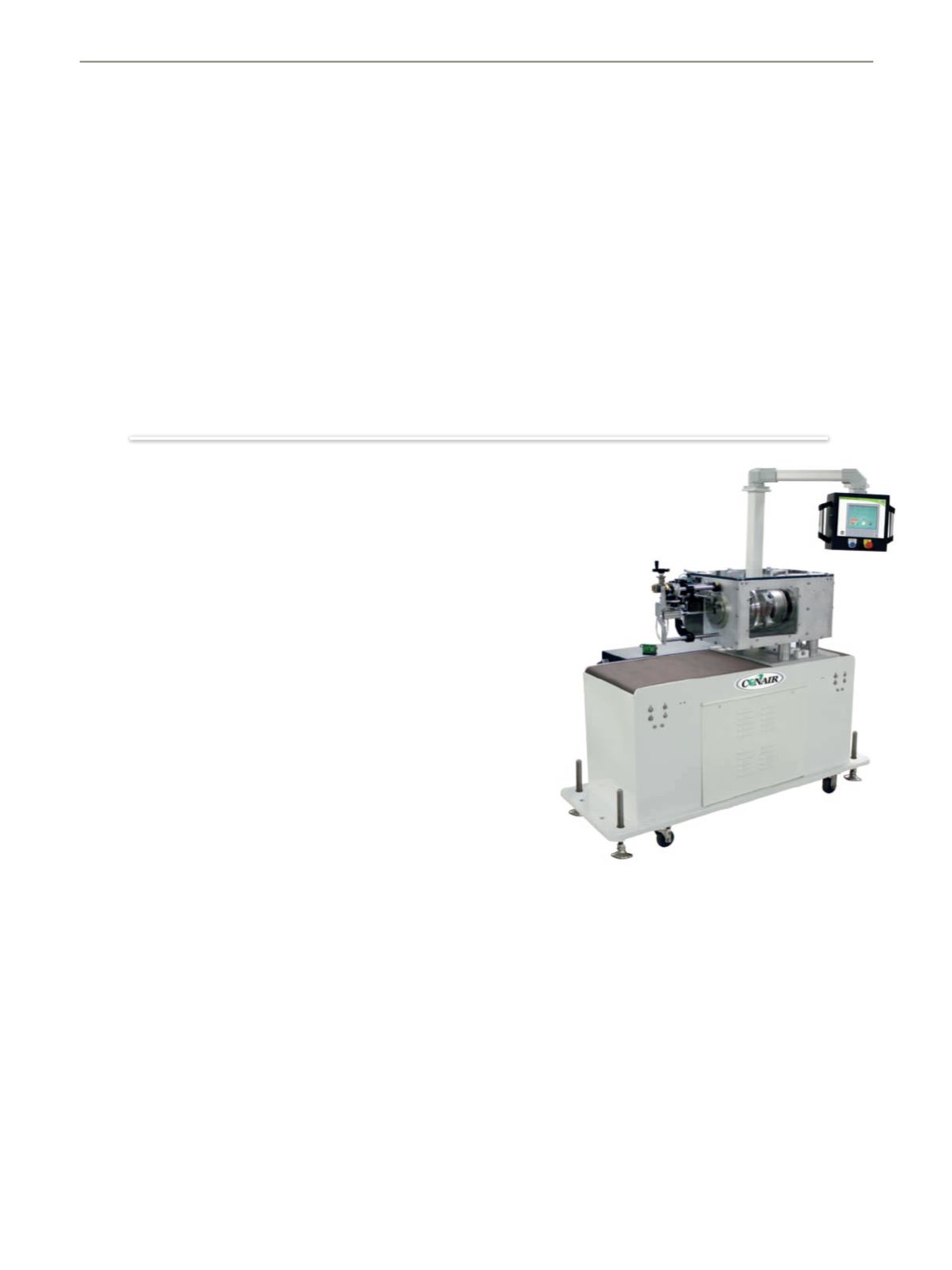
(30.5 m/minute). The cutter’s
standard servo controls enable
it to make distortion-free and
particulate-free cuts at rates
up to 45 per minute while
holding cut-to-length toleran-
ces of ±0.031 inch (±0.787
mm), even on shorter lengths
of tubing. The cutter can be
used with the full range of me-
dical plastic tubing, including
difficult-to-cut materials such
as styrene, PET, HIPS, and PC.
The M-TPC cutter features a front-moun-
ted touchscreen control that enables an
operator to set table travel velocity, tub-
ing size, blade velocity, and cutting
depth. Once created, specific cutting
programs or ‘recipes’ can be stored in
on-board memory for easy recall and re-
use. The cutter is engineered to allow for
quick blade changes without the need to
remove product from the machine, so
the need to stop and restart the line for
blade replacement is eliminated.
“The Conair M-TPC cutter was develo-
ped to eliminate the need for secondary
cutting and finishing in the production of
precision medical tubing,” explains Bob
Bessemer, Medical Downstream Extrusi-
64
kompakt
Extrusion 5/2017
automated defect recognition (ADR) and
computed tomography (CT) in a single
unit. VisiConsult automated these pro-
cesses with an ABB robot to achieve
higher throughput and reduce labor
costs. The system can be placed directly
at the production line to take parts from
a tray, conveyor belt or similar and places
them inside the cabinet. The system is
one of the first combined in-line ADR
and CT systems allowing a hundred per-
cent 3D analysis of the parts. Typical
checks are wall thickness analysis, poro-
sity analysis or nominal-actual-compari-
son. This makes such a system the per-
fect choice for high-volume and safety
relevant industries like automotive.
The compact X-ray cabinet InSpect can
be used with Mini-Focus or Micro-Focus
tubes and film, imaging plates (CR) or di-
gital detectors to generate high resoluti-
on images of samples. The compact
form factor allows usage in laboratories,
technology centers and even quality
checks of samples on the production
floor. Due to the flexible choice of image
sources the system can be customized
towards customer requirements and
budget. The embedded screen directly
shows inspection results and allows
high-end image processing within a few
clicks to achieve outstanding results.
Comprehensive archiving options to da-
tabases, PACS servers, file systems or re-
ports allow users to store their results.
The intuitive operation allows highest ef-
ficiency.
Beside the XRH111+Robot and the In-
Spect VisiConsult has a lot more inspecti-
on systems based on X-ray technology in
its product portfolio.
➠
VisiConsult X-ray Systems &
Solutions GmbH
www.visiconsult.de➠
The Conair Group
www.conairgroup.comn
A new, patent-pending medical travel-
ing planetary cutter (M-TPC) from Conair
features a fully-programmable, servo-
driven cutting head that cuts small-dia-
meter medical plastic tubing so precisely
that the need for secondary, off-line tube
finishing is virtually eliminated. The pla-
netary knife spins around the circumfe-
rence of tubing from 0.080 to 1 inch in
outside diameter (2.03 to 25.4 mm OD),
cutting it without deformation, particula-
tes, burning or fracturing.
The M-TPC cutter, the latest in the
Conair MedLine
®
family of cleanroom-
ready, downstream extrusion equipment
for medical applications, has been intro-
duced at Plastec East in New York.
Unlike other cutters that remove tube
material and can leave particulates be-
hind, the M-TPC planetary cutter actually
splits the tubing apart cleanly through
displacement, without the loss of any
material. This cutting method never
blocks continuous airflow through the
center of the tube, so tube sizing and
ovality are not affected as they can be
when flying-knife cutters are used. The
programmable, servo-driven cutting
head enables complete and precise con-
trol of cutter speed (surface speed), rate
of cutter penetration (feed speed), and
final depth of the cut.
The planetary cutter is mounted on a
precision, servo-driven traveling table
that can handle tubing automatically at
line speeds of up to 100 ft/minute
Micro Planetary Cutter
The new, patent-pending medical travel-
ing planetary cutter (M-TPC) from Conair
features a fully-programmable, servo-
driven cutting head that cuts small-diame-
ter medical plastic tubing so precisely that
the need for secondary, off-line tube
finishing is virtually eliminated
on Sales Manager for Conair. “Given the
added level of blade control, and the abi-
lity to lubricate the cut using alcohol, the
M-TPC cutter makes it possible to achie-
ve an almost perfect cut.
For applications that require even tighter
cut-to-length tolerances than those pro-
vided by the standard servo-controlled
cutter, the M-TPC can be fitted with an
optional dead stop that maintains cut-to-
length tolerances of ±0.005 inch
(±0.127 mm) or less. A switch initiates
the cut cycle, starting table travel and
clamping the tube so it comes to rest
gently against the physical stop before
being cut precisely.