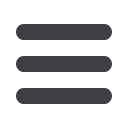
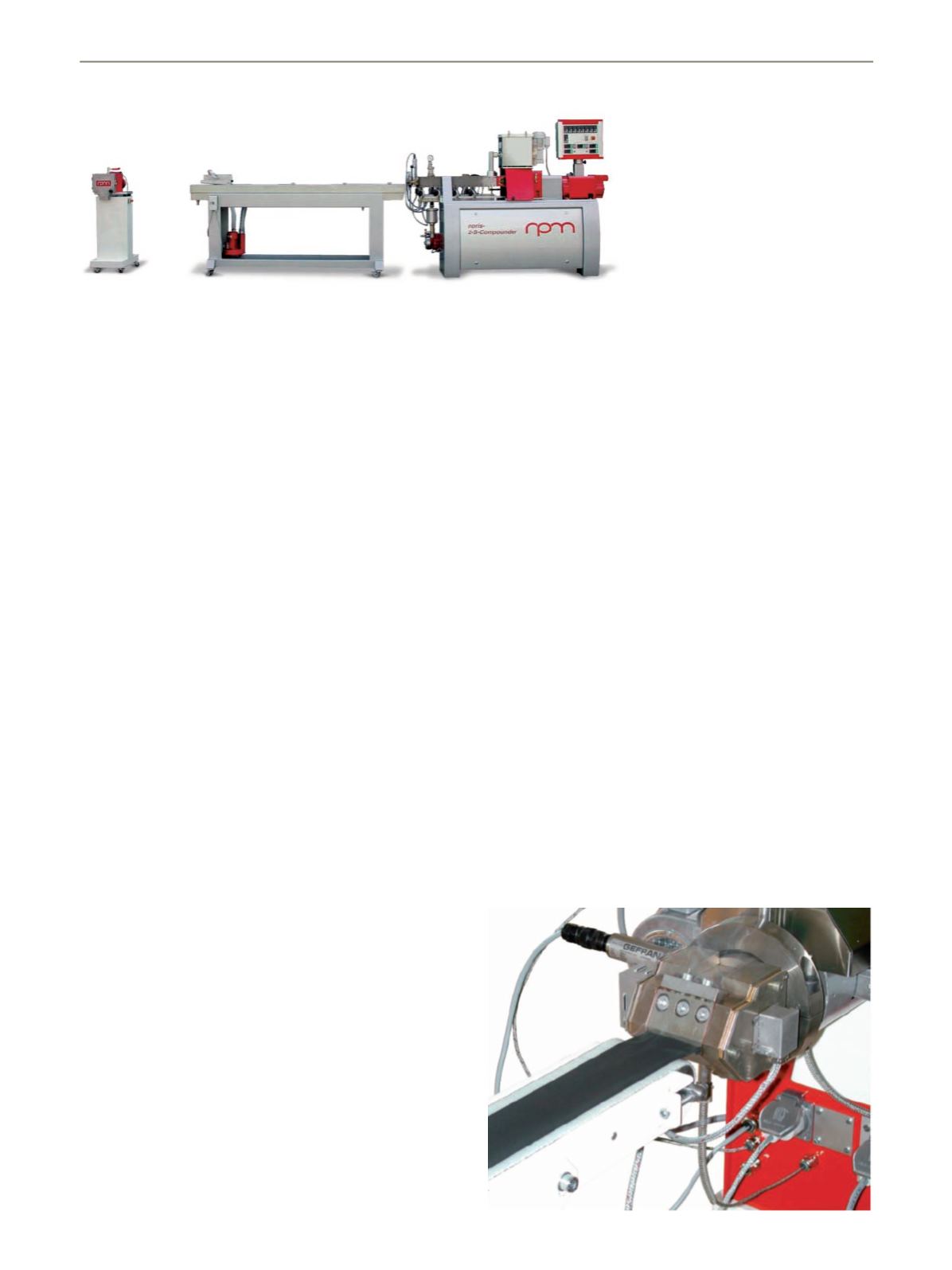
45
Extrusion 6/2016
Nach Abschluss meines Studiums und der Tätigkeit bei Loewe
Opta wurde ich bei Mobil Oil Deutschland als beratender Inge-
nieur verpflichtet. 1964 wechselte ich zur Maschinenfabrik Paul
Leistritz in Nürnberg und begann dort mit dem Aufbau eines
neuen Produktbereiches Extrusionstechnik. Das bedeutete, ich
begann bei „null“ mit der Entwicklung, Produktion und Ver-
trieb von Ein- und Doppelschneckenextrudern.
Bei der Firma Leistritz haben Sie die Compoundier-
Technologie kennen gelernt – eine Technologie, mit der
Sie beinahe Ihr ganzes Leben lang verbunden sind.
Tenner
: Mit dem Eintritt in die Firma Leistritz begann für mich
das Thema „Kunststoff und Kunststoffverarbeitung“, einer
neuen und für mich schwierigen Dimension. Gleichzeitig be-
gann damit auch die Kontaktaufnahme mit dem Thema
Masterbatch. Auf der Suche nach geeigneten Einsatzgebieten
für die bei Leistritz entwickelten und hergestellten Doppel-
schneckenextruder entdeckten wir den Bereich Masterbatch.
Für die Herstellung von hochwertigen Masterbaches waren
Maschinen erforderlich, die eine hohe Dispergierqualität bei au-
ßergewöhnlicher Mischqualität ermöglichen. Zu dieser Zeit
standen uns nur Kenntnisse über gegenläufige Doppelschne-
ckenextruder zur Verfügung, da die für diese Aufgabe besser
geeigneten gleichläufigen Extruder noch patentrechtlich ge-
schützt waren.
Durch geeignete Schneckenkonfigurationen und Entwickelung
von Misch- und Homogenisierelementen gelang es uns, auch
gegenläufige Doppelschneckenextruder erfolgreich für diese
Aufgabe einzusetzen. Eine komplette Anlage bestand wie
Bild 1
zeigt aus einem Vormischer, dem Extruder mit Dosierung,
einem Siebwechsler für die Abscheidung von Grobteilchen, die
entweder als Fremdkörper oder durch die verwendeten pulver-
förmigen Pigmente vorhanden waren.
Nach dem Granulierdüsenkopf folgen Strangkühlwanne mit
Strangtrocknung, Granulator, Klassierung und Zwischensilo.
Derartige Anlagen wurden in einem Leistungsbereich zwischen
30 und 300 kg pro Stunde eingesetzt.
Ist kein Feinmahlgut für das Polymer vorhanden, muss ein Teil
des gesamten Polymeranteils, zum Beispiel 50 Prozent, über ei-
ne Feinmahlanlage zu einer Korngröße von circa 50 µm zerklei-
nert werden. In Verbindung mit dem nichtzerkleinerten Poly-
mer kann diese Mischung als Ausgangsmaterial mit gutem Er-
folg verwendet werden.
In der Anfangsphase der Masterbatch-Fertigung wurden vor-
zugsweise einfache Farben wie schwarz, weiß, grün etc. herge-
stellt. Aber die Welt wurde immer bunter und die Anzahl der
geforderten Farbeinstellungen wuchs rasant. Für die Herstel-
lung dieser vielfach in kleineren Chargengrößen benötigten
Konzentraten werden häufig Anlagen gemäß
Bild 2
eingesetzt.
Der Vorteil dieser Maschine liegt bei ihrer universellen Ver-
wendbarkeit, das heißt hier können Schneckenkonfigurationen
Zylinderaufbau und andere Parameter der Aufgabe angepasst
werden. Neben der geringen Investitionskosten einer derarti-
gen Maschine ist ein weiterer Vorteil durch diese Art der ver-
wendeten Baukastenschnecke und -zylinder die schnelle Um-
rüstbarkeit auf geänderte Verarbeitungsparameter bzw. -mate-
rialien. Deshalb hat auch dieser Labordoppelschneckenextruder
bzw. Compounder, wie er in Zwischenzeit bezeichnet wird, ei-
ne außergewöhnliche umfangreiche Einsatzbreite gefunden.
Neben der Herstellung von Farbmasterbatches können derarti-
ge Anlagen auch für die Herstellung von Additivmasterbatches
aller Art, zum Beispiel Stabilisatorenbatch, Gleitmittelbatch,
Korrosionsschutzbatch etc. hergestellt werden. Im Zuge der
Weiterentwicklung können Batches aller Art mit derartigen An-
lagen hergestellt werden.
Farbmetrische Prüfungen sind relativ aufwendig, so dass oft-
mals eine Kontrolle mittels Prüfstreifen als Alternative dient.
Diese über Einschneckenprüfextruder extrudierten Prüfstreifen
oder Prüffolienmethode ermöglichen einen einfachen und un-
komplizierten Vergleich der erreichten Farbqualität mit dem
Farbwunsch. Ein Detail einer derartigen Anlage zeigt
Bild 3
.
Diese Anlage besteht aus einem Einschneckenprüfextruder, ei-
nem Streifenextrusionswerkzeug und einen Abzugsband.
Bild 2: LAB Stranggranulier-
Anlage
(Quelle: Noris Plastic)
Bild 3: Bandabzug (Quelle: Noris Plastic)